CSUN student uses 3D printing passion to help healthcare workers
Sako Chekerjian, a sophomore, holds a strain reliever. Chekerjian said it takes up to 3 hours to make 5 ear guards.
August 14, 2020
When the announcement to wear face masks became mandatory at the end of March, there was a shortage of personal protective equipment and it became harder to find masks, such as N95 masks.
This left many healthcare workers having to purchase their own or even risk caring for patients without one. The shortage concerned many individuals, including CSUN sophomore Sako Chekerjian.
Chekerjian,19, and his friend Riley Ravi, 18, a UC Berkeley freshman, have been printing faceshield headbands and ear guards with a 3D printer to donate to local hospitals. The pair have so far donated 60 face shields they assembled using their 3D-printed headbands and plastic sheets to health workers at the Keck School of Medicine of USC.
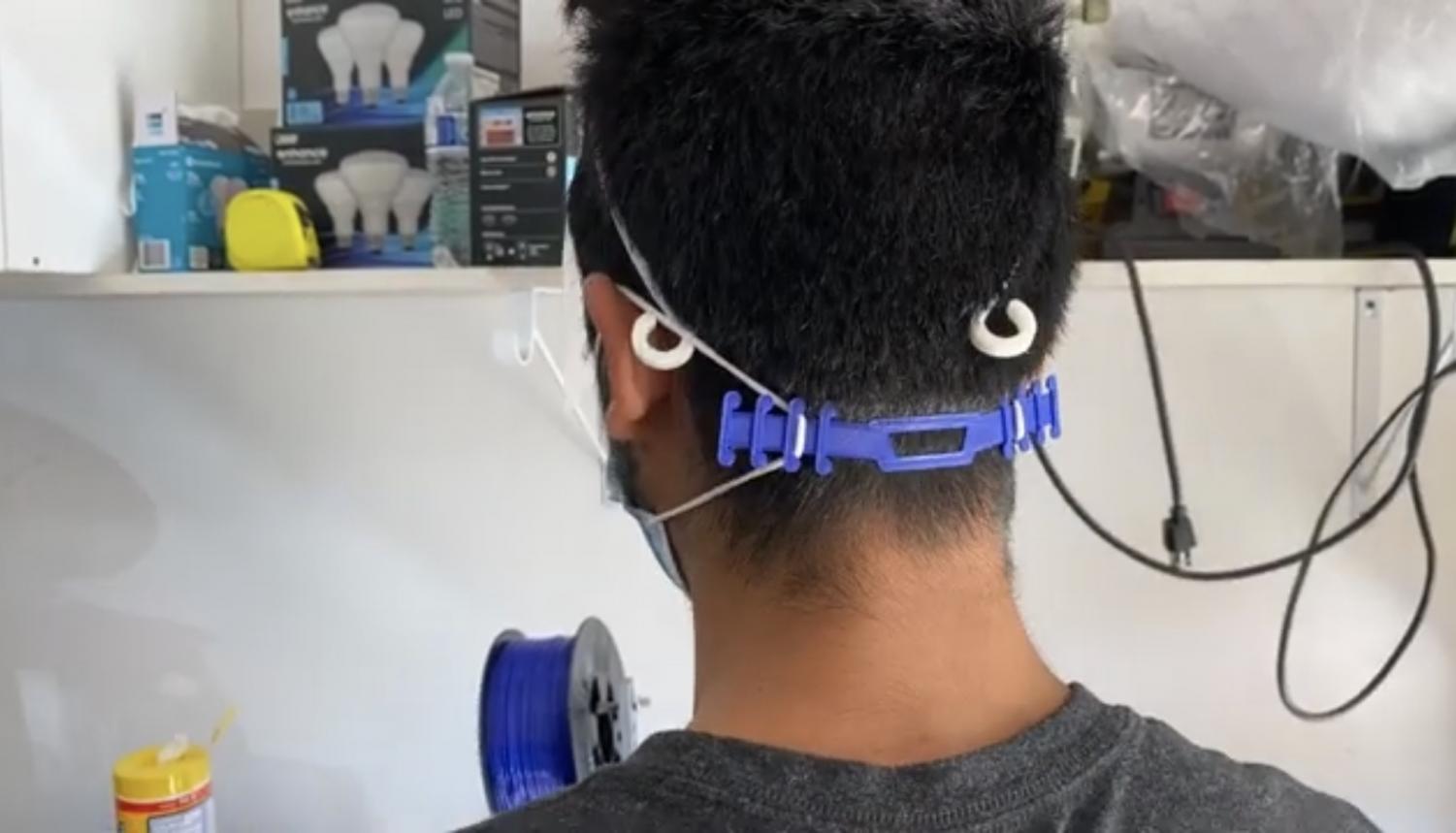
“One of the main reasons I wanted to start doing this was because I saw on the news about hospitals not having enough equipment and doctors and nurses paying their own money to get masks, and the closest thing I can do to make masks, is make face shields,” Chekerjian said. “I’m trying to get in contact with them (hospitals) and say, ‘Hey, I can make equipment’ and I can get my friends to start making equipment and start this whole mass production.”
The elastic ear loops on facemasks can cause strain on a wearer’s ears after a long period of usage. To ease the strain, medical workers have been using ear guards — simple devices that go behind the head to hold the two elastic bands in place and relieve stress behind the ears.
“It actually feels as though I’m not wearing a mask at all,” Chekerjian said.
Chekerijian has been 3D printing ear guards — a process that takes about 3 hours to print 5 ear guards — in his home garage. He has around 100 ear guards sitting in a box ready to be sold or donated.
Chekerjian said he and his friends have been trying to donate the ear guards to hospitals, but haven’t received many responses from hospitals interested in them. Many hospitals require the ear guards to be built in a safe environment, which is why Chekerjian wears gloves and makes sure his work area is sanitized. Chekerjian also sells the guards to the public on Etsy.
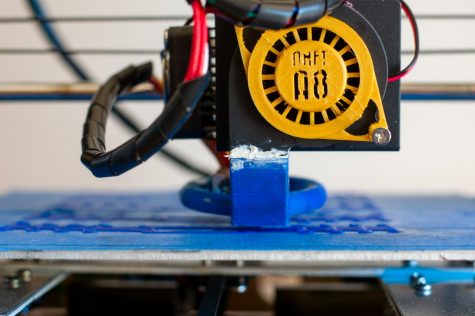
Chekerjian’s 3D printer gave him the opportunity to use his passion for engineering to help nurses and doctors.
“My passion is engineering and this is something closest to it and the best part of a 3D printer is that it has all those aspects of engineering,” Chekerjian said. “When you start 3D printing, it’s going to become a hobby if you really enjoy it. It has to be something that you enjoy and you have time and patience for. This is a project I wanted to look into.”
Chekerjian said a 3D printer needs a lot of patience and research to maintain.
Chekerjian has two 3D printers that cost him hundreds of dollars in his home’s garage in Glendale. Each roll of 3D printer filament he uses to create the ear guards costs $20.
“You have to be aware of every single part of it because things can go wrong when you’re not watching it,” Chekerjian said. “Worst case scenario is it catching fire because it could go up to 392°F. So you need a lot of patience to make sure that the printer is at the quality you need and making sure the printer is healthy before you start printing.”
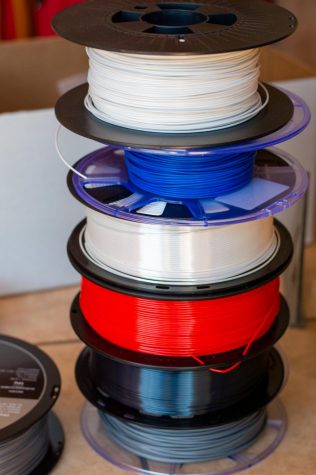
Chekerjian was part of his high school’s robotics club and his interest carried with him after graduating and starting his education at CSUN.
“What really interested me is 3D printing, so when I graduated high school, I used my money to buy a really cheap one just to learn the basics. I had to assemble the whole thing and I had to manually put this together,” Chekerjian said. “Every day, I was working on it. I even stopped playing video games because I wanted to work on it.”
Before the pandemic, Chekerjian joined Sunrise Los Angeles, an organization and movement that is made up of young inspired individuals who advocate and bring awareness to climate change.
“In Sunrise L.A. there’s people of color, people who just graduated from college, undergrad. It’s very diverse,” Chekerjian said.
Chekerjian said he wanted to bring the organization to CSUN and host an art event on campus, but the pandemic put that idea on hold.
He has given back to the community in more ways than 3D printing ear guards for donation. Last month, Chekerjian volunteered at a food distribution event in Echo Park.
“There’s a lot of people out there that are trying to make money and are not as privileged as a lot of us,” Chekerjian said. “So just going out there and doing something little. When we went it was a joy to see people gather and grab food.”
Chekerjian said the younger generation wants to help others who don’t have the same opportunities they do.
“I feel like the people that we look up to, they’re not helping, so we just have to do it ourselves,” Chekerjian said.
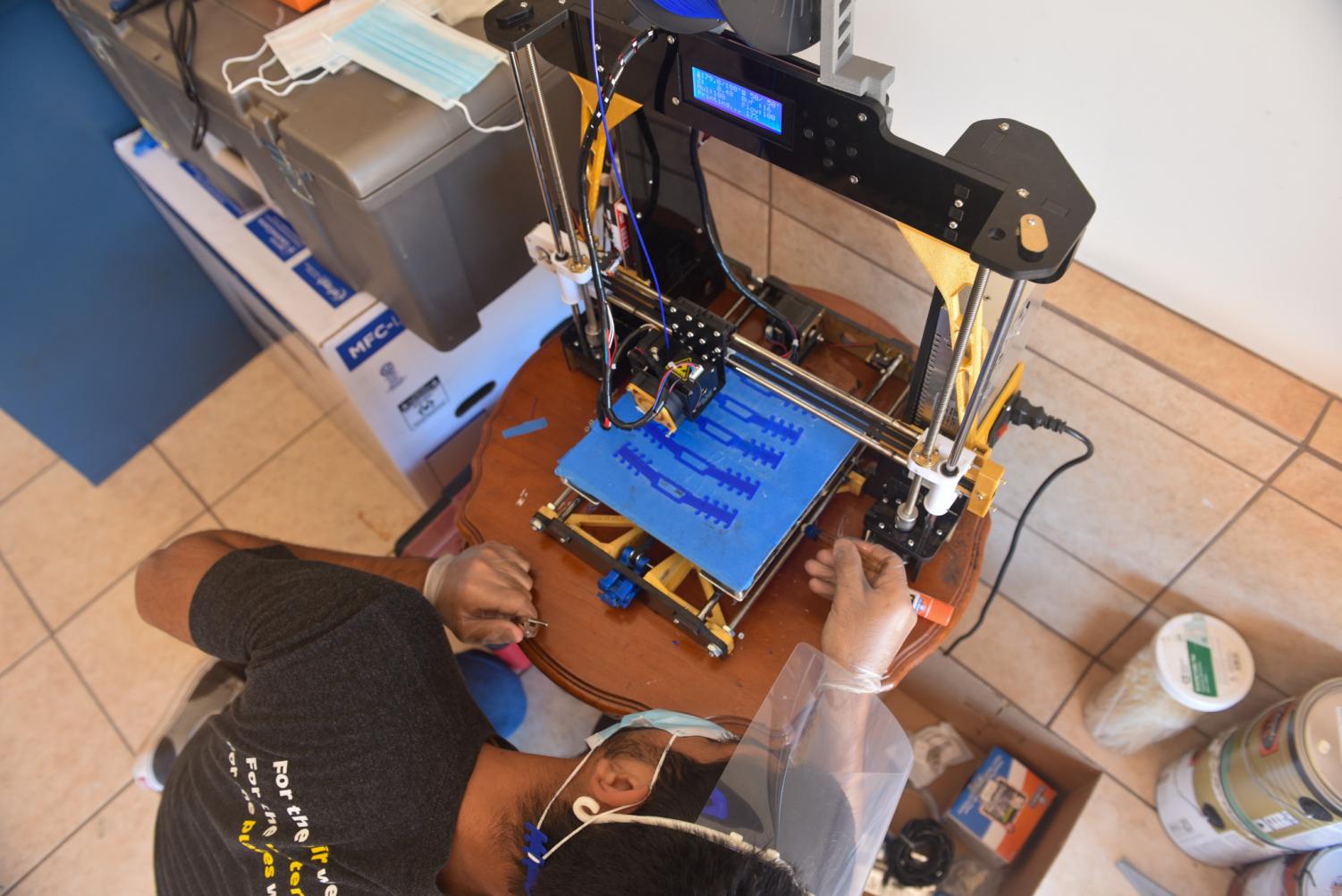